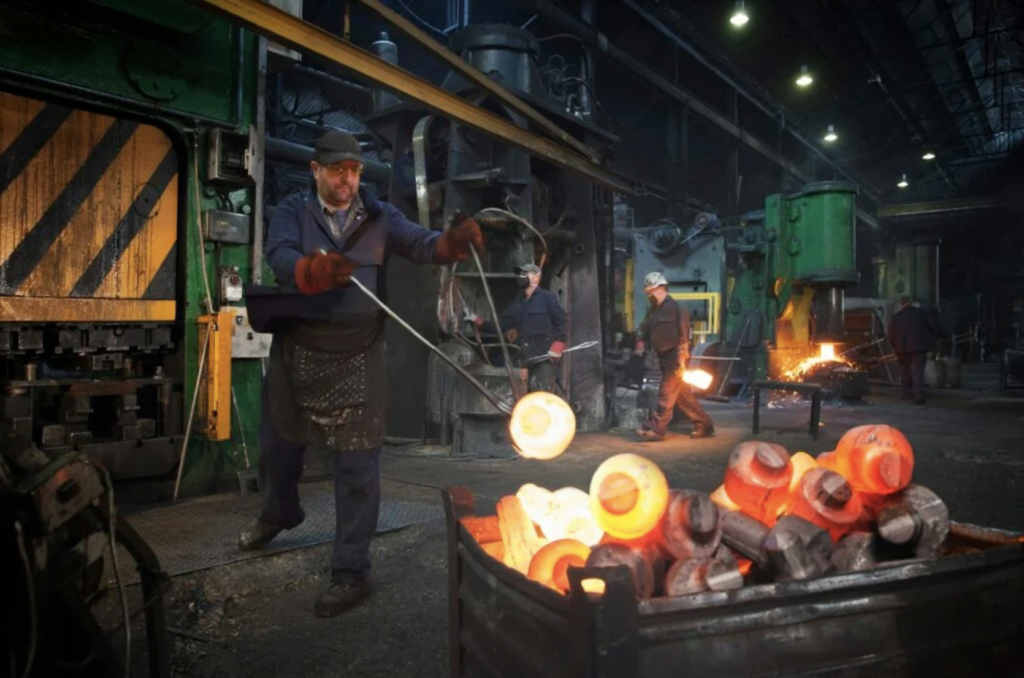
Forging is all about applying pressure to metal billets, allowing them to deform plastically into the desired shapes. This method enhances the mechanical properties of the material, eliminates common casting defects like porosity, and strengthens the metal. For this reason, forged parts are often used in critical applications where heavy loads and tough operating conditions are the norm.
The Typical Application of Forged Components
Forged components play a significant role across various industries. Here’s a breakdown of how forging is utilized in different sectors:
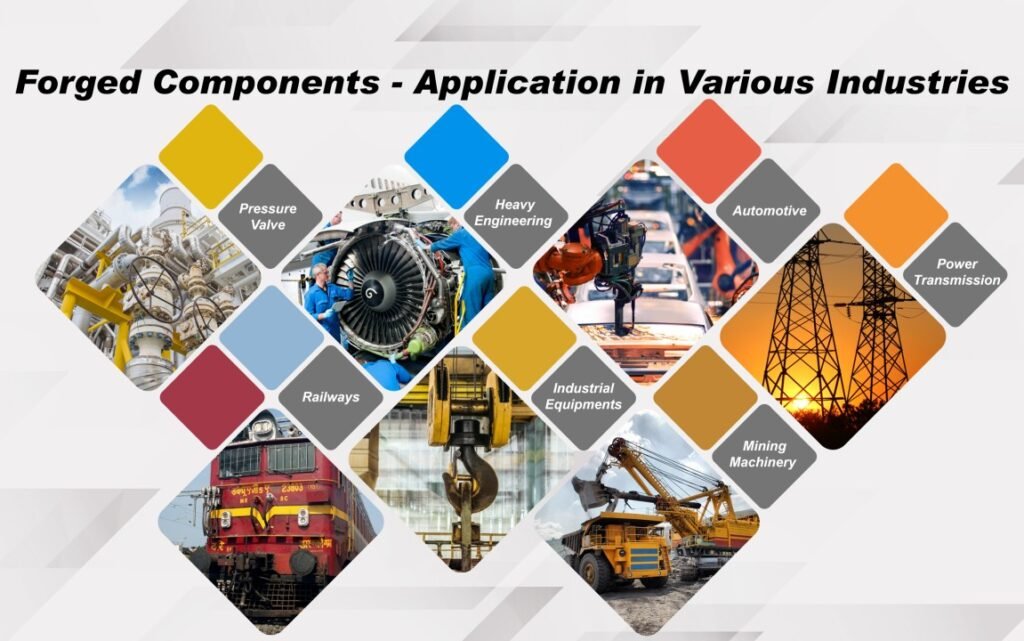
- Defense Industry: Did you know that forged parts comprise 85% of an aircraft’s weight and 70% of a tank’s weight? That’s because critical components like those used in cannons and firearms must be robust and reliable.
- Machinery Manufacturing: Forging is key to producing spindles, drive shafts, gears, and cutting tools—essential parts in the machinery manufacturing process.
- Power Generation: Major power generation components, like turbine main shafts, impellers, and rotors, are produced by forging, ensuring these parts can withstand high stresses over time.
- Transportation: Many of the components in locomotives and cars—such as axles, connecting rods, front beams, and crankshafts—are forged for strength and durability. Even excavator teeth are forged to ensure they can handle intense wear and tear.
- Agriculture: The agricultural sector relies on forged parts for tools like plow blades and forks in modern tractors. These parts need to be both strong and long-lasting to handle heavy-duty work.
- Everyday Tools: Even in daily life, we see the importance of forging in common tools like wrenches, hammers, and knives, all of which are designed for strength and durability
What is Metal Preforming?
The term “preform” refers to the initial shape or form that a metal takes before undergoing final manufacturing processes like forging, machining, or pressing. These components are produced using various methods, such as casting, forging, powder metallurgy, and even 3D printing, depending on the intended application and material.
The role of metal preforms in modern manufacturing cannot be understated. They allow industries to reduce waste, save costs, and produce more complex shapes that would be difficult or inefficient to make through traditional machining alone. By providing a pre-shaped metal, manufacturers can achieve near-final geometries with minimal material removal and reduced labor.
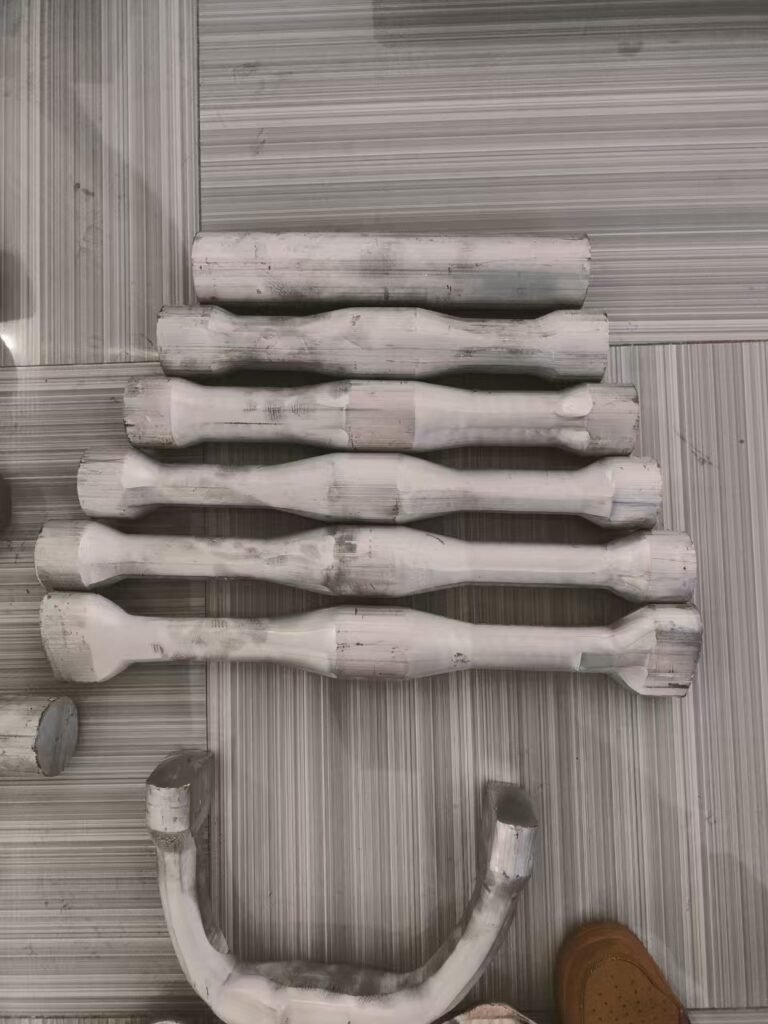
Our Commitment to Precision in Metal Pre-Forming
We QLM Forging provide metal pre-forming solutions for customers who need both precision and efficiency in their forging works. We focus on two primary types of machines: roll forging machines and cross wedge rolling machines, which are designed for elongating critical components such as crankshafts, automotive suspension parts, U-arms/connecting rods, and knuckles. These machines ensure that parts achieve the ideal strength-to-weight ratio, making them both strong and lightweight.
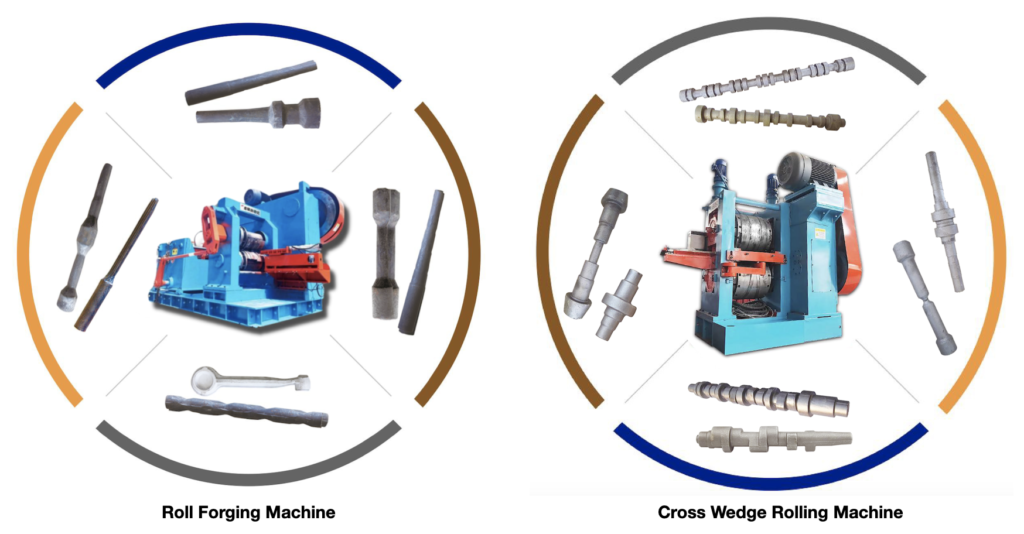
On the other hand, cross wedge rolling machines have a standout feature: one single die can forge out two pieces simultaneously, offering unmatched precision and enhancing work efficiency. This process not only allows for mass production but also ensures that each component meets strict quality standards with minimal waste.
Tailored Forging Solutions for Diverse Industries
With extensive experience serving partners in the forging industry, we are able to provide the most practical solutions for customers. By analyzing the 3D product drawings, we can expertly design the die and select the machine type to efficiently accomplish your forging tasks.
Our deep industry experience is a vital invisible value, helping you avoid costly errors and saving your budget.

